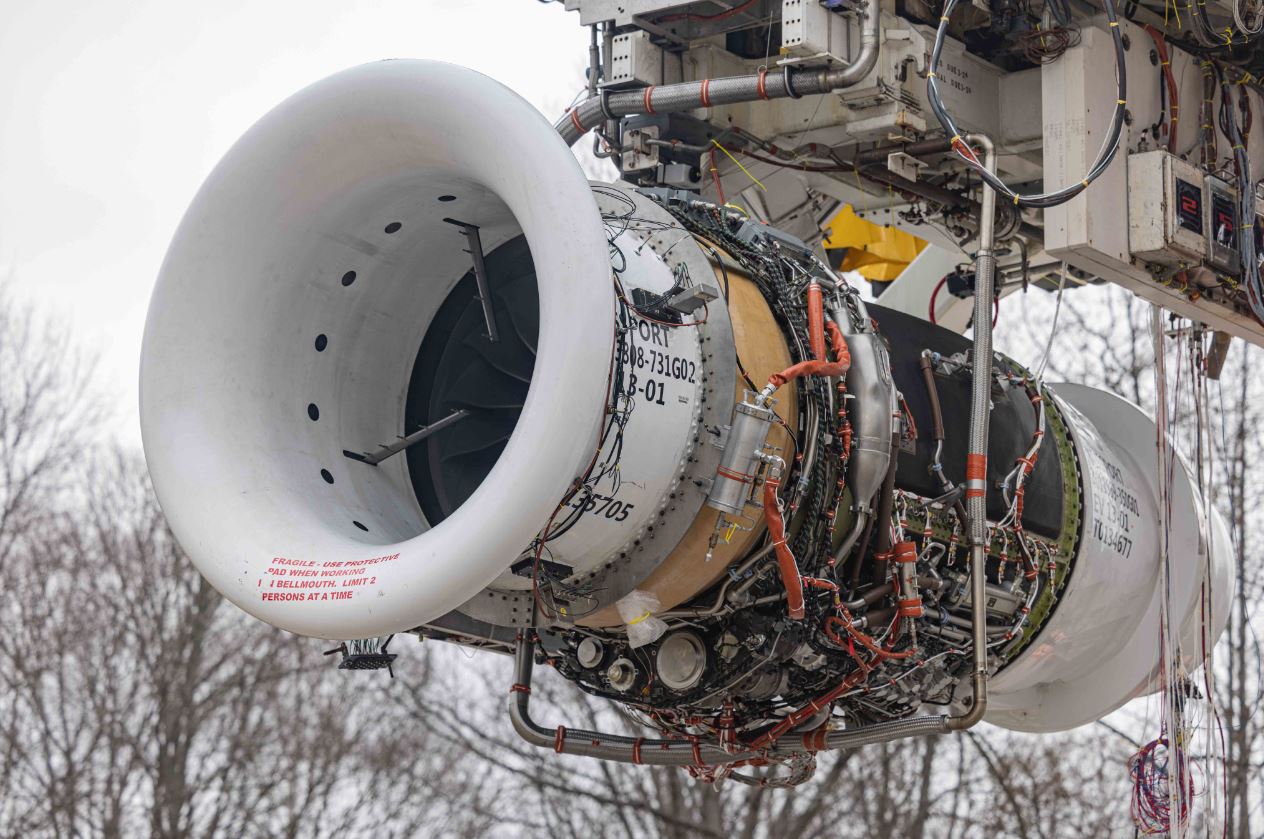
A Passport engine during baseline testing in 2024 at GE Aerospace’s Peebles Test Operation in Ohio for the HyTEC Turbofan Engine Power Extraction Demonstration.
GE Aerospace will soon begin testing hybrid electric components on a modified Passport ultra-long range business jet engine as part of its collaboration with NASA’s Hybrid Thermally Efficient Core (HyTEC) project. The goal is to develop a more sustainable powerplant that lowers fuel burn and improves power extraction.
Baseline tests for the HyTEC Turbofan Engine Power Extraction Demonstration have already been completed at GE Aerospace’s Peebles Test Operation in Ohio, and initial component-level testing of electric motor/generators and power electronics has been finalized at the company’s Electrical Power Integrated Systems Center, or EPISCenter, in Dayton, OH.
The GE Aerospace / NASA HyTEC project is emblematic of the aviation industry’s collaborative spirit to be more sustainable. In fact, business aviation’s CLIMBING. FAST advocacy initiative is on a mission to help the industry achieve net-zero carbon emissions by 2050.
The demonstrator engine is now being assembled at the company’s headquarters in Evendale, OH, and final tests on the modified Passport engine are expected to begin soon.
“This testbed is going to be both a performance demonstrator and a controls demonstrator. We are integrating multiple motor generators to prove out the control of hybrid electric technologies and verify the performance of the turbofan and hybrid electric system when they’re integrated together,” said Mike Millhaem, GE Aerospace systems leader for the HyTEC power extraction demonstrator.
“We’re going to be pushing the engine to a lot of places where it wasn’t originally designed to go. There are physics-based limitations on gas-powered turbofans, and these tests will show us how hybrid electric components can change the engine cycle so that we’re able to operate the engine with less fuel during certain phases of flight,” Millhaem continued.
“This testbed is going to be both a performance demonstrator and a controls demonstrator. We are integrating multiple motor generators to prove out the control of hybrid electric technologies and verify the performance of the turbofan and hybrid electric system when they’re integrated together.”
MIKE MILLHAEM, GE Aerospace systems leader
These tests will deliver crucial insights on how electric power can improve efficiency and reduce emissions in aircraft engines, Millhaem added. “We’ve got decades of data on how pure gas-powered turbofans operate, but for hybrid electric technologies, we are working with physics-based modeling estimations. This demonstrator test finally allows us to benchmark this technology with fundamental empirical data on what the engine cycle does when augmented with hybrid electric components,” he explained.
GE Aerospace has also structured the HyTEC Turbofan Engine Power Extraction Demonstration to be battery agnostic, which could help accelerate the introduction of hybrid electric technologies prior to energy storage solutions being fully matured. “There are a lot of cycle efficiency improvements we can make with just hybrid electric components on the engine. Then, if we get to the point where there is an energy storage solution that is competitive from a weight standpoint, this technology can be fully integrated with that energy storage system,” Millhaem noted.
“Our collaborations with industry partners like GE Aerospace are paving the way for U.S. leadership in hybrid electric commercial transport aircraft.”
ANTHONY NERONE, HyTEC project manager, NASA’s Glenn Research Center
The HyTEC Turbofan Engine Power Extraction Demonstration is part of GE Aerospace’s contribution to Phase 1 of NASA’s HyTEC project, which focuses on high-pressure compressor and high-pressure turbine advanced aerodynamics, as well as engine combustors. NASA recently awarded GE Aerospace a contract for Phase 2 of the HyTEC project to continue developing technologies for an aircraft engine core demonstrator test later this decade.
“Our collaborations with industry partners like GE Aerospace are paving the way for U.S. leadership in hybrid electric commercial transport aircraft,” said Anthony Nerone, HyTEC project manager, NASA’s Glenn Research Center.
Data from this demonstrator test is also informing the CFM International Revolutionary Innovation for Sustainable Engines (RISE) program. Unveiled in 2021, the RISE program encompasses a suite of pioneering technologies, including advanced engine architectures like Open Fan, compact core, and hybrid electric systems to be compatible with 100% or unblended sustainable aviation fuel.
CFM International is a joint venture between GE Aerospace and Safran Aircraft Engines, each owning 50% of the engine maker.
“The HyTEC Turbofan Engine Power Extraction Demonstration is showcasing some tremendously exciting technology, and we’ll be conducting tests that have never been done before,” said Millhaem. “We continue to push the envelope forward; it’s a great time to be an aerospace engineer.”